ロジスティクスとは何か?物流管理とは違う?メリット・デメリットと、実例を交えて解説!
ロジスティクスとは
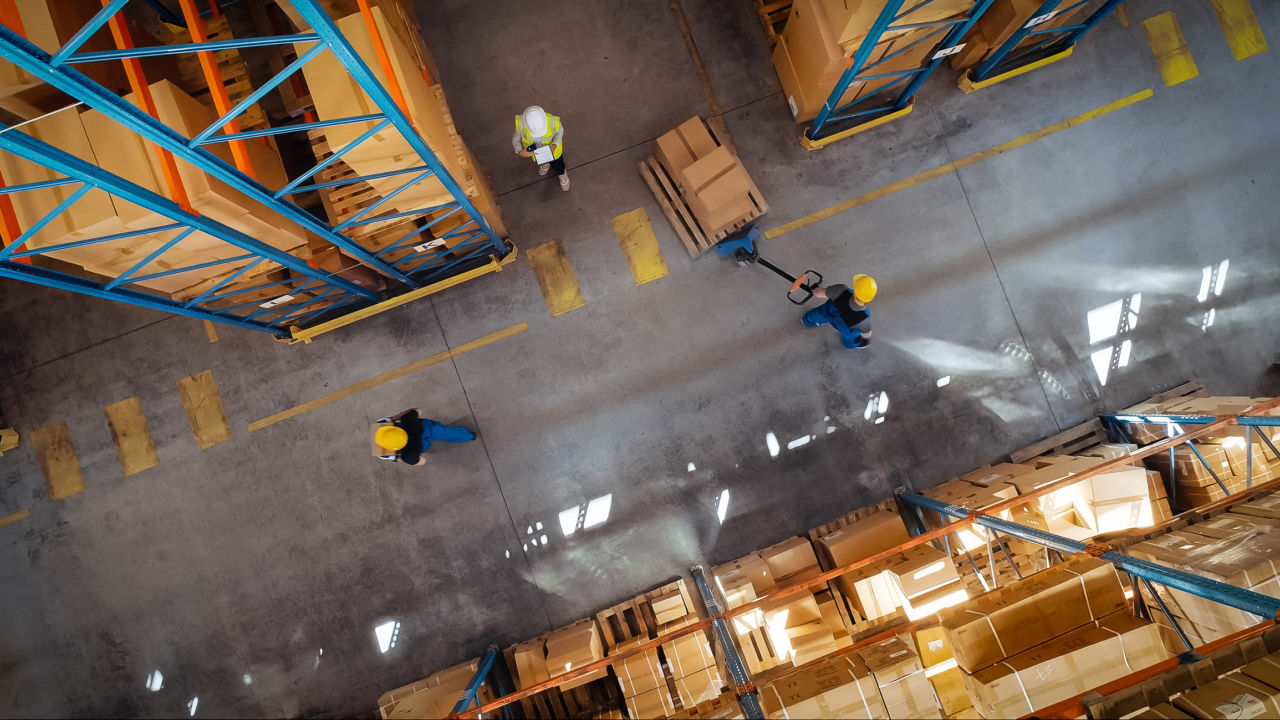
ロジスティクスとは、原材料や部品の調達からエンドユーザーへの販売までを含めた、商品供給一連の流れをマネジメントする仕組みである。
一般的には「ロジスティクス=物流管理」と捉えられがちだが、両者の概念は大きく違う。物流管理は、運送・荷役・保管・返品・入出庫・受発注・在庫といった業務プロセスのマネジメントを意味し、各業務プロセスの円滑な運営と効率化を主な目的とする。
一方でロジスティクスでは、購買・研究・生産・営業・販売といった組織・部門を巻き込んで、物流機能の高度化をめざす。それだけでなくロジスティクスは、需要・供給や納期の最適化を視野に入れる。
ロジスティクスはもともと軍事用語で、兵站つまり前線への兵員・燃料・兵器の補給を意味する。近代戦では、作戦の良し悪しよりもロジスティクスの優劣が勝敗を決するという考えもある。現代の企業間競争においても、同じことがいえる。経営やマーケティングの戦略はもちろん大切だが、そもそもロジスティクスがきちんと機能してなければ競合に勝つことはもちろん、生き残ることさえ難しいのだ。
ロジスティクスのメリット
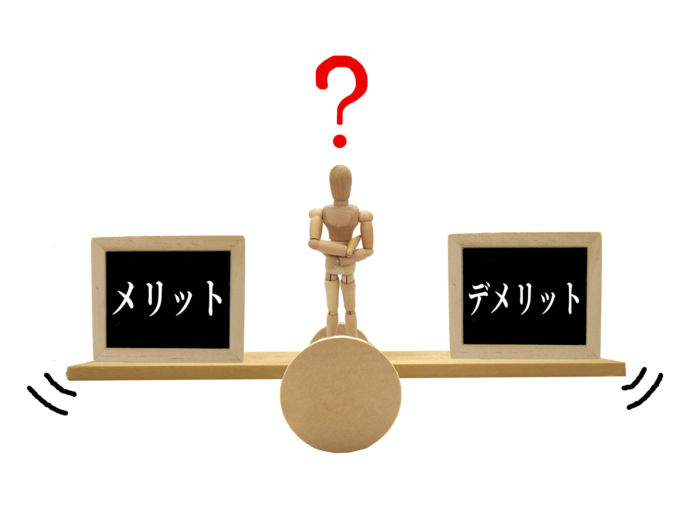
ロジスティクスのメリットとしては、機会損失の極小化と在庫陳腐化抑制の抑制が挙げられる。
機会損失の極小化
2021年4月、「まるでジョッキビールの味わい」と評判を呼んだ「アサヒスーパードライ 生ジョッキ缶」が、発売後わずか2日間で販売を休止した。あまりの売れゆきに商品供給が追いつかなかったためだ。
「生ジョッキ缶」ほどではないが、新製品や季節品では受注予測が上振れして欠品が続出、結果として機会損失を生むということがしばしば起こる。ロジスティクス体制の強化により、受注動向に応じて商品供給をフレキシブルに対応させることができれば、こうした機会損失も極小化できる。
在庫陳腐化の抑制
機会損失が極小化できたとしても、在庫が膨らんでは本末転倒だ。最後には売れ残って陳腐化し、せっかく作った商品が廃棄に追い込まれる。
特殊な生産工程、調達困難な資材……こうしたボトルネックが過剰在庫を生む。ロジスティクスの強化はこうしたボトルネック解消の切り札となりうるのだ。
ロジスティクス導入のデメリット
ロジスティクス導入のデメリットは、コストにある。最上流のサプライヤーから購買・生産・物流・マーケティング・営業そして最下流の販売チャネルまでを連携させる一気通貫のシステムを構築するには、莫大なコストがかかる。また、物流施設などの整備・統合など、ハード面での投資も重くのしかかる。
直接的なコストではないが、ロジスティクス導入に欠かせない業務プロセス見直し、社内の意識浸透、マネジメント層まで巻き込んだ意思決定プロセス革新なども多大な時間と労力を要する。これだけのハードルを乗り越えるには、「是が非でもロジスティクスを根付かせる」とする経営トップの強い覚悟とリーダーシップが欠かせない。
ロジスティクス取り組みの実例
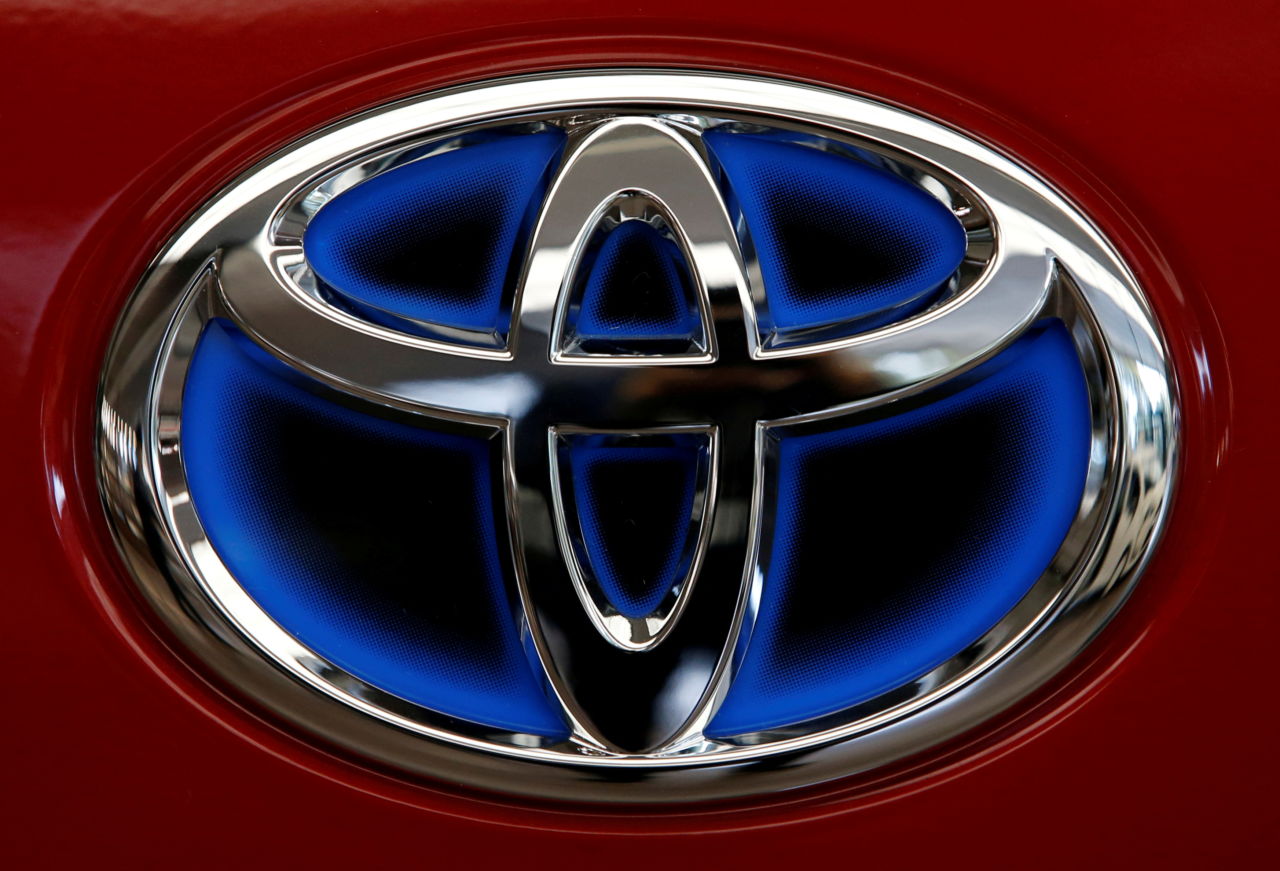
ロジスティクス取り組みの実例として、自動車メーカーの半導体不足問題について取り上げる。
2021年、自動車メーカー各社は「半導体部品が足りず自動車が製造できない」事態に陥った。コロナ禍で落ち込んだ販売が北米・中国市場を中心に急回復したにもかかわらず、半導体の調達がボトルネックとなって生産を抑えざるを得なくなったのだ。
最近の自動車は、センターラインに沿って自動的にハンドルを操作したり、前方の障害物を感知してブレーキをかけたりといった運転支援システムを搭載している。コンソールパネルも、もはやスマホ画面さながらのつくりだ。そして、これらの電子機器には大量の半導体が使われている。半導体は今や、自動車生産に欠かせないキーパーツなのだ。
こうした状況で、底力をみせたのがトップメーカーのトヨタ自動車(愛知県)だ。同社はサプライヤーと連携し、半導体のように調達に時間がかかる部品のひっ迫に備えてきた。だからこそ、多くの自動車メーカーが減産や工場の稼働停止に追い込まれた中で、トヨタ自動車だけは影響が限定的だったとされている。