原価計算とは?原価計算をするとどう役に立つ?メリット・デメリットを徹底解説!
原価計算とは
原価計算とは、工場で発生する材料仕入れ・設備投資・作業スタッフの雇用などにかかるコストを各製品1個あたりに配分するプロセスである。
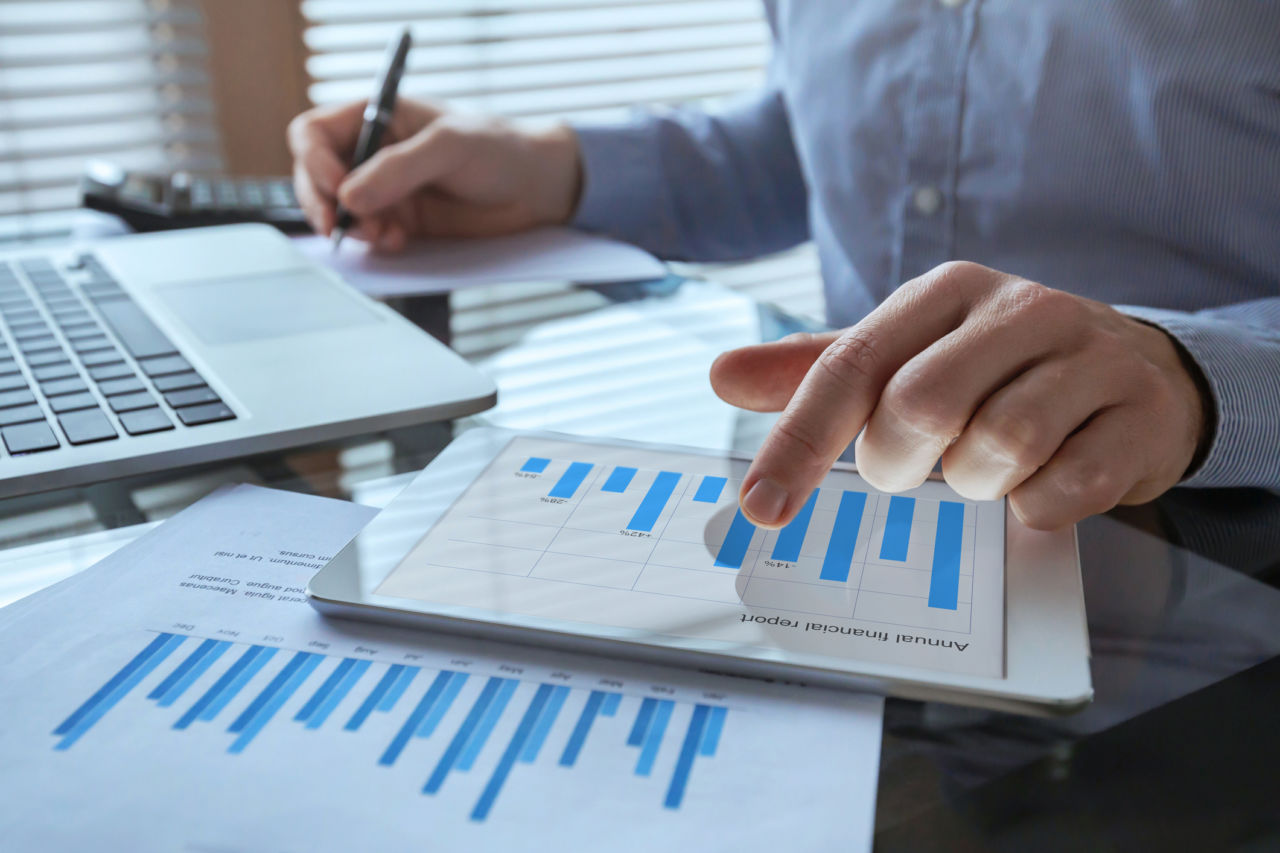
原価計算のメリット
原価計算のメリットは、経営・事業活動の意思決定や生産活動での業績評価に役立つ点にある。
当初の原価計算は、いわゆる在庫金額の計算など会計上のアプローチを主な目的としていた。製品の販売価格を決める際に、原価を指標とすることもあった。当時の原価計算は、実際に支出した費用を製品1個に配分する「実際原価計算」が主流だった。
大きく流れが変わったのが20世紀初頭のアメリカだ。単なる会計上のツールとしての原価計算は「原価管理」へと脱皮を遂げる。科学的管理法産みの親フレデリック・テイラーが標準原価計算を提唱したのだ。その頃ちょうど、T型フォード車の大量生産が始まり、ベルトコンベアーによる分業工程が今までの職人のモノづくりに取って替わる。
標準とは、「あるべきスタンダード」だ。標準原価計算では、工数・日産量・歩留まり・稼働時間といった生産要素が標準として設定される。そして実生産において標準・実績の差異を検証し、生産性の足を引っ張る原因をつぶす……標準原価管理は工場での生産性向上・コスト低減に大きく寄与した。
標準原価計算は、設備投資の効果金額や新製品損益の試算などにも活用でき、経営判断にも役立つ。
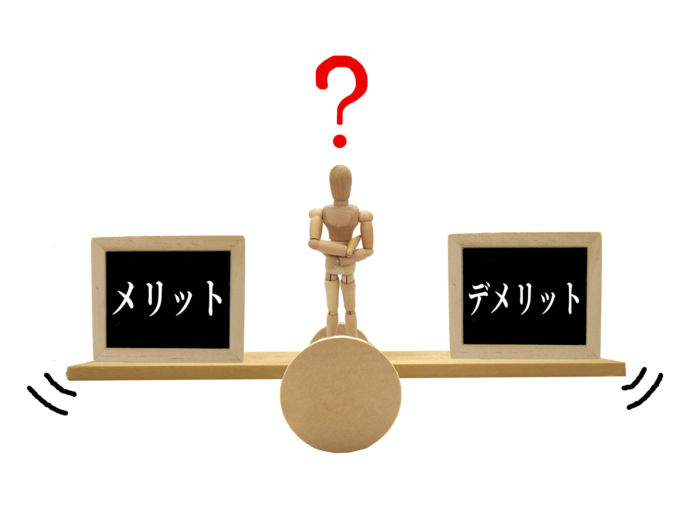
原価計算のデメリット
原価計算のデメリットは、計算に労力がかかること、その割には正しい原価の算定が難しいことにある。原価は、会計情報と非会計情報を組み合わせて計算する。「何にいくらかかったか」といった会計情報は、システマチックに収集できる。
大変なのは、非会計情報だ。設備稼働実績(稼働時間や停止要因)、ロット別作業工数実績、材料の要因別不良、完成品の歩留まり、検査不合格率とその要因…原価を弾き出すのに欠かせない情報ばかりだが、収集する現場スタッフに負担がかかる。当然快く引き受けてくれるとは限らない。
集めた情報に基づき、製品ごとに原価を振り分ける作業も手間がかかる。しかも、いきなり製品原価を弾き出すのではない。たとえば自動車なら、プレス・溶接・塗装・エンジン製造(鋳造・機械加工・熱処理・パーツ組み込み)・組み立てといった工程別に原価を算定したうえで積み上げなければ完成品の原価は出てこない。
気の遠くなる作業の果てに原価を算出した後にも、「正しい原価」というハードルが待ちかまえる。工場でかかるコストのうち、部品の仕入れコストなどは製品ごとの原価として捉えやすいが、設備や人件費などの共通費は個々の製品に振りかえるのが難しい。
原価計算では、一定の前提条件をもとに共通費を製品物に無理やり配分する。パンデミックによる年間生産計画落ち込みなどのように前提条件が大きくずれると、原価の納得性も失われる。つまり「使えない原価」をわざわざ苦労して弾き出したことになるわけだ。
原価計算の実例
原価計算の実例として、トヨタ自動車(愛知県)の取り組みについて紹介する。「カイゼン」の元祖として知られるトヨタの原価低減は卓抜しており、コロナ禍に見舞われた2000年度も原価低減効果1500億円が寄与して競合を寄せ付けない高い収益を叩き出した。
そして、原価低減活動のベースを支えるのが原価計算のしくみだ。トヨタは現場と経理部門がチームを組み、まずワークセンター・MCT(マシンサイクルタイム)などの業務標準を整備してきた。同時に、原価計算結果をカイゼンに活かすPDCAの仕組みを作り上げている。
さらに最近では、IoT(Internet of Things:モノのインターネット)を通じて、設備稼働情報などをリアルタイムかつ労力をかけずに収集できるようになった。トヨタの原価計算は、日々進歩しているのだ。